Authentic craftsmanship
The primary material for making most rugs is sheep wool. The sheep are sheared twice a year, in spring and at the end of summer, by an experienced shepherd using hand shears or a special clipper. Most often, it is nomadic herders who tend to large flocks of sheep, primarily raised for their soft, precious fleece.
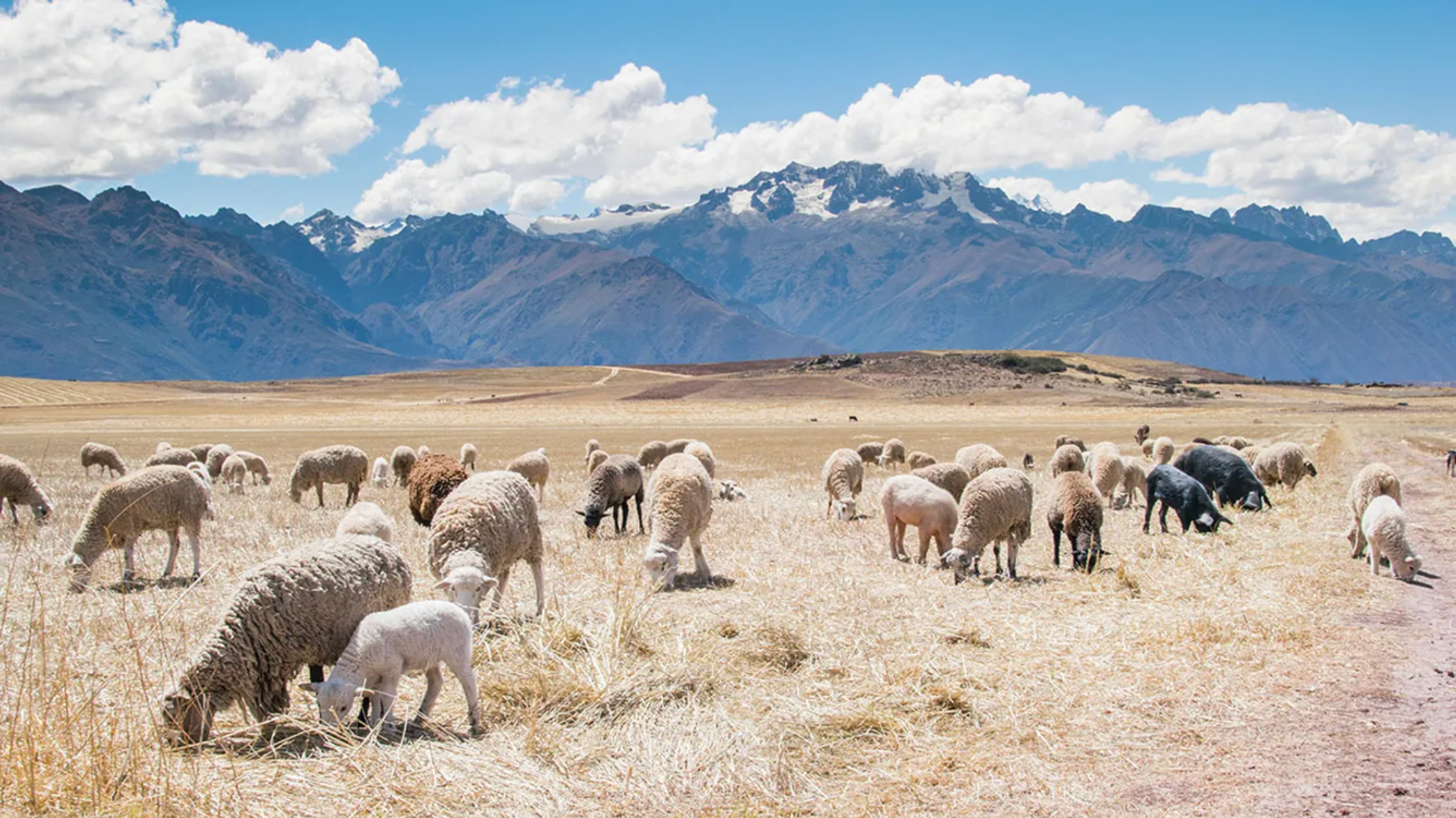
Sheeps
The natural fat content in Persian wool makes it highly resistant to dirt and moisture. The wool also has a beautiful natural sheen. There are thousands of sheep breeds worldwide, each with different wool properties. This particular breed is known as "carpet sheep", and its high-quality wool contributes to the exceptional durability of the rugs.
Sorting, washing, drying, carding, spinning, and twisting are the essential steps that wool must undergo before it can be used as finished yarn for rugs and carpets.
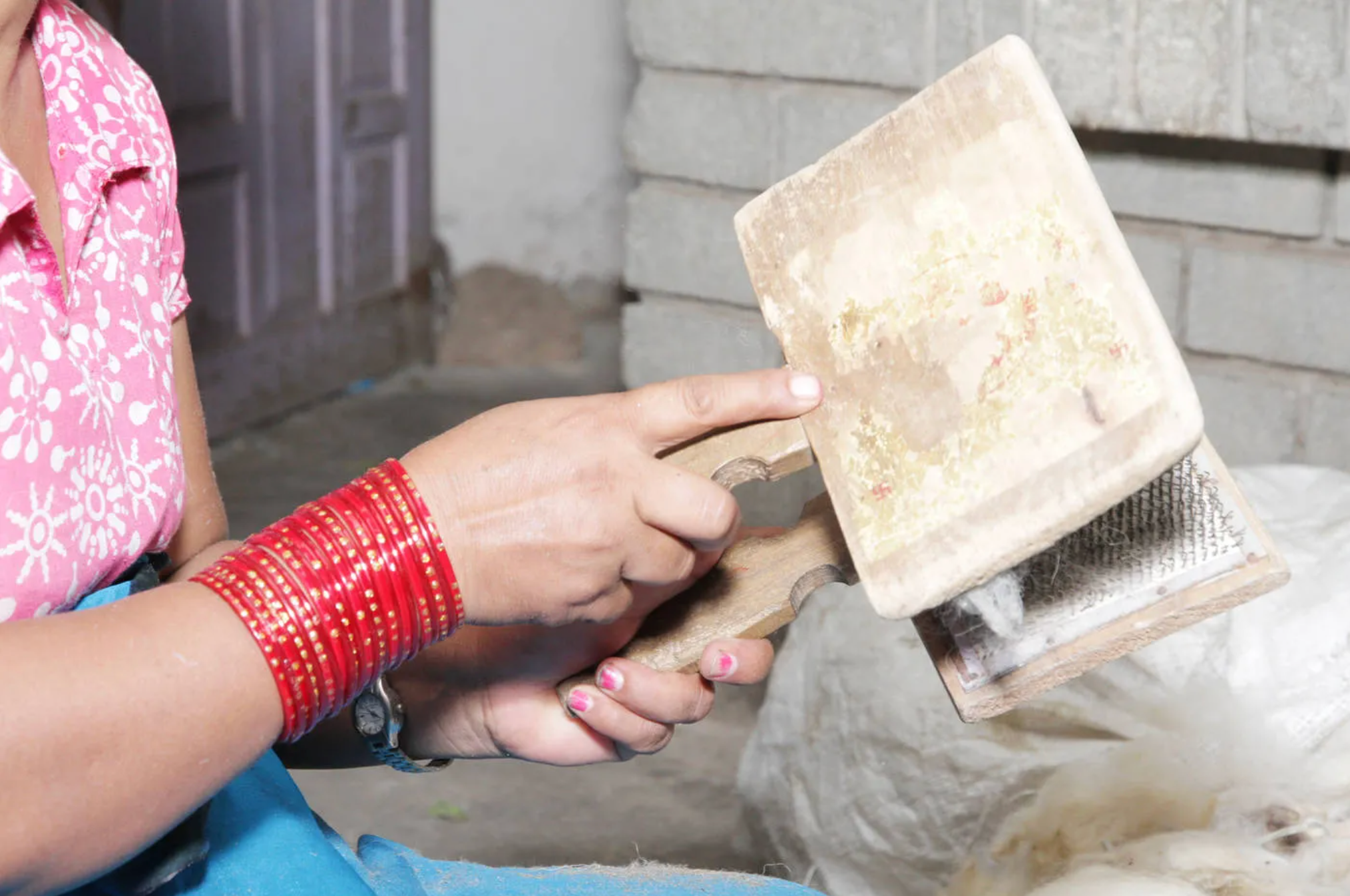
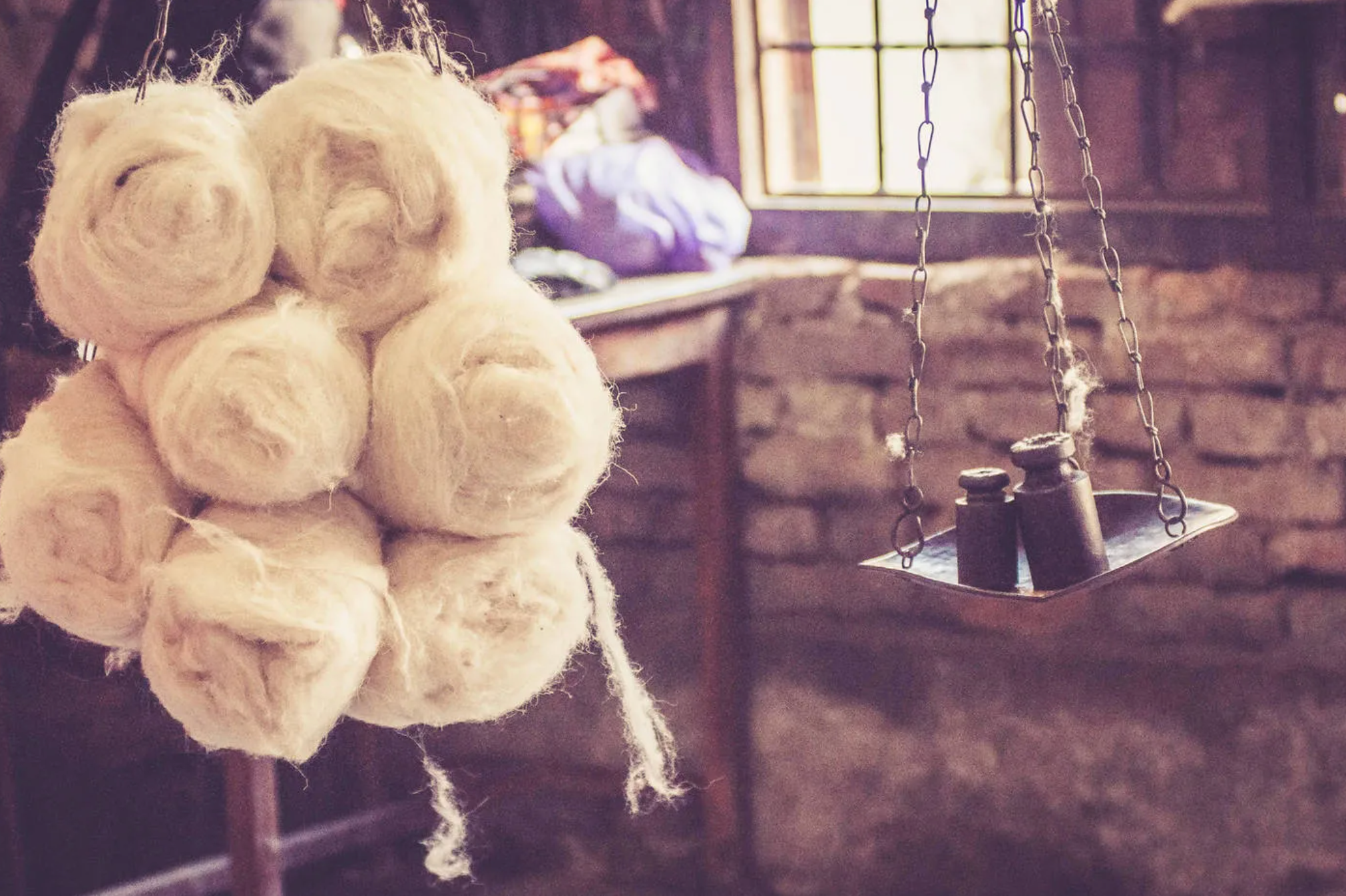
Processing the Wool: From Raw Fiber to Finished Yarn
The process begins with sorting the wool into different categories. Wool from ewes, lambs, and rams must be kept separate and cannot be combined into a single yarn strand.
After sorting, the wool is washed and beaten with sticks—a traditional method used to remove dirt and impurities. The cleaned wool is then spread out to dry under the sun, often on riverbanks or in open fields.
Once dry, the wool is ready for carding. Using a chubug (a long wooden stick), the wool is beaten again to further loosen the fibers. Women then meticulously untangle the fibers and remove any remaining debris using special carding brushes, preparing the wool for the next stages of spinning and weaving.
After carding, the wool is ready for spinning. This process is traditionally carried out by women using age-old tools: a simple drop spindle and a more advanced spinning wheel.
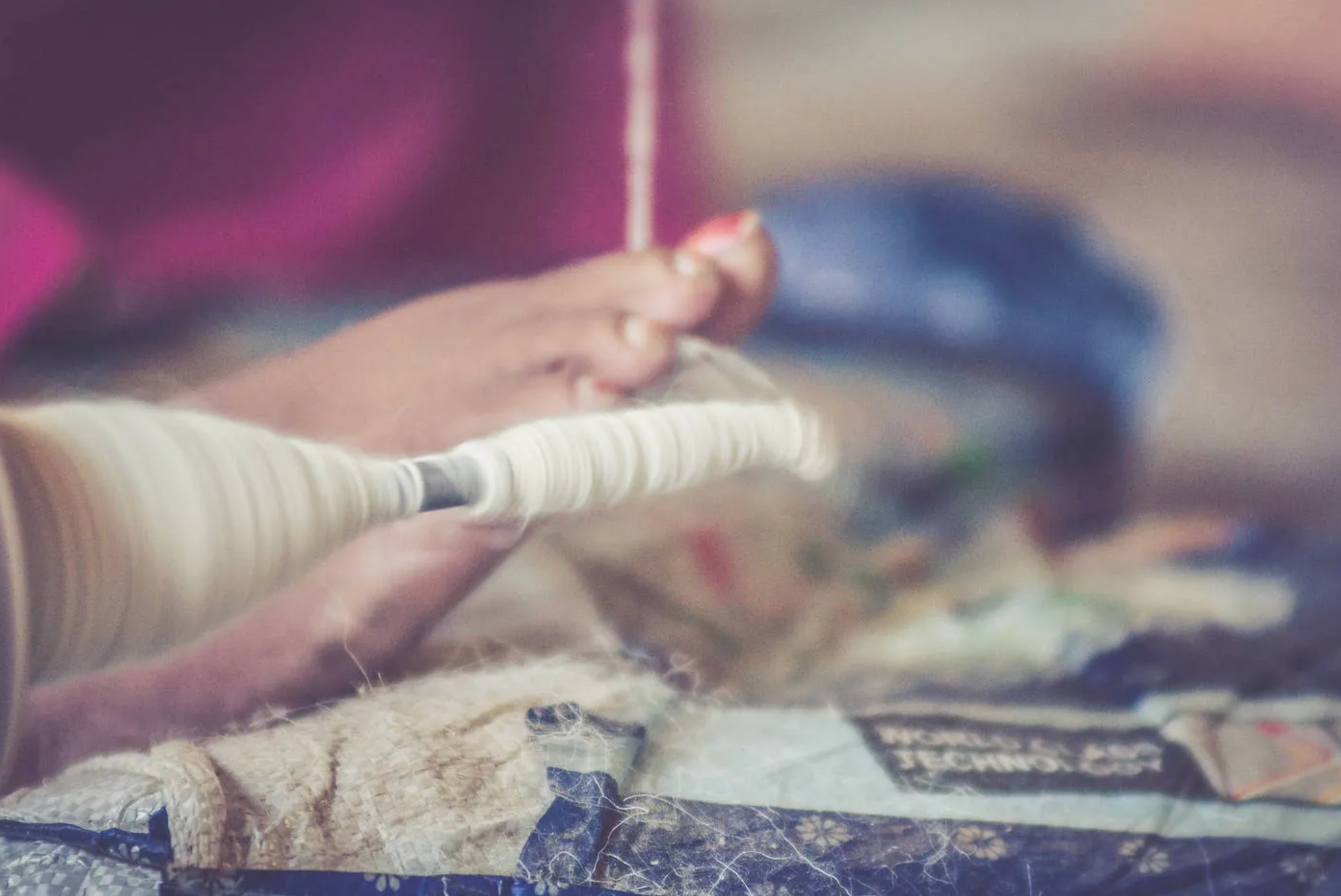
Spinning and Twisting: The Art of Transforming Wool into Yarn
Spinning with a drop spindle requires immense skill, precision, and a delicate touch. As the fiber passes through the spinner’s hands, it must be simultaneously drawn out, twisted, and wound around the spindle rod. If the yarn is spun poorly, it becomes weak, more prone to breaking, and uneven in texture, which can result in inconsistent dye absorption.
Weak yarn is completely unsuitable for setting up the warp threads on a loom, as these serve as the foundation of the rug. High-quality spinning is therefore essential to ensure the durability, strength, and beauty of the final woven piece.
A spinning wheel is a more modern and possibly more efficient tool from the cities and knotting workshops. After spinning, the threads are sometimes combined into a stronger whole. The process of combining the fibers is called twisting.
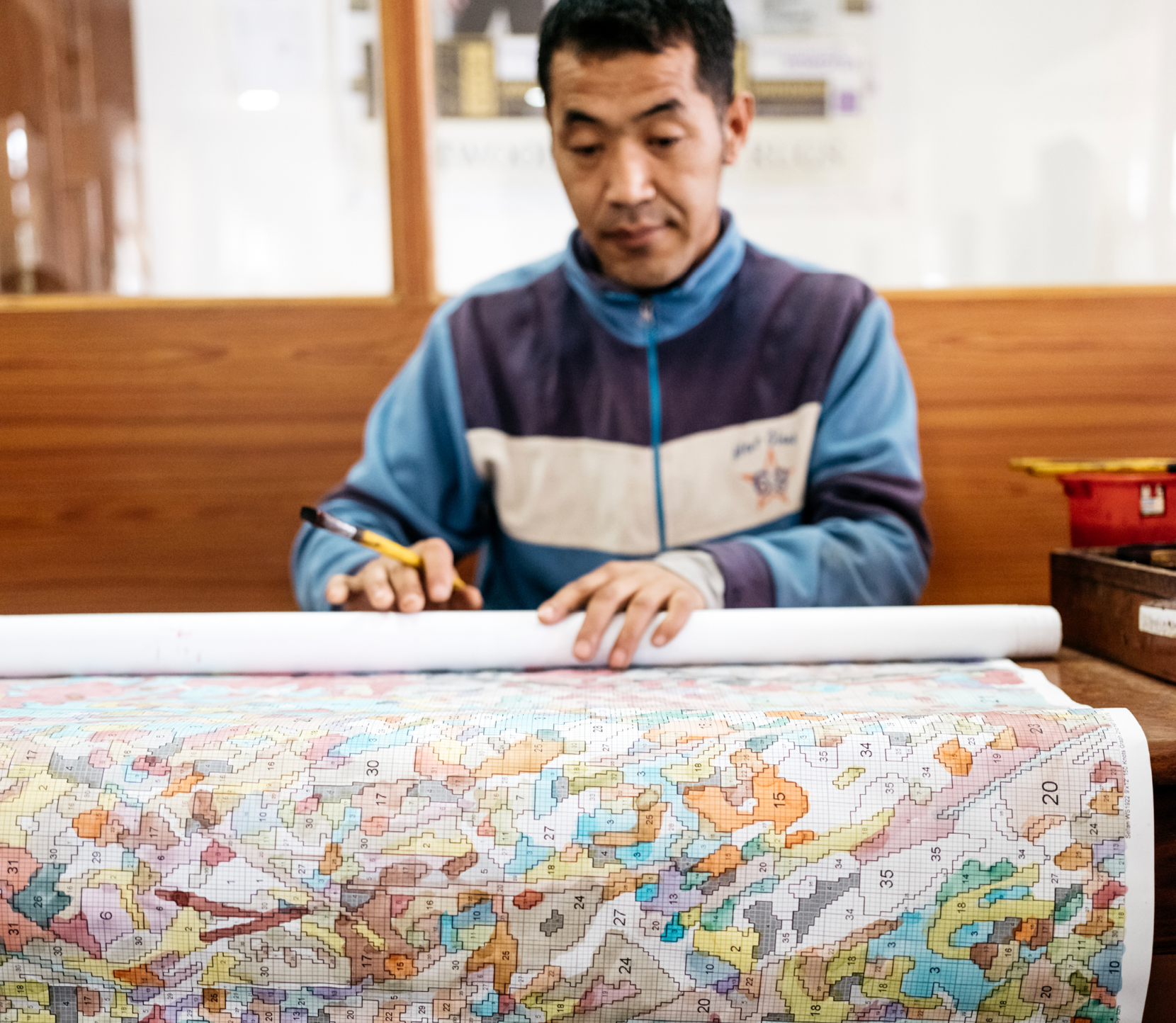
Sketching
Sketching, calculating, painting, and preparing a loom are also crucial steps in the production process. For each new carpet design, a knotting plan must be created as a guide for the weavers. The design drawing is made by a master draftsman on millimeter paper and colored. This requires a great deal of skill and precision. Sometimes, codes and numbering are assigned to the patterns so that the weavers can interpret them according to the legend.
An accurate price estimate is important, which is why digital raw material and material calculations are done in modern weaving mills before the knotting process. The goal is to get an overview of the final production costs and to minimize losses. Once the sketch is finished and the amount of material needed to complete the carpet has been determined, all this data is collected and handed over to the dye master.
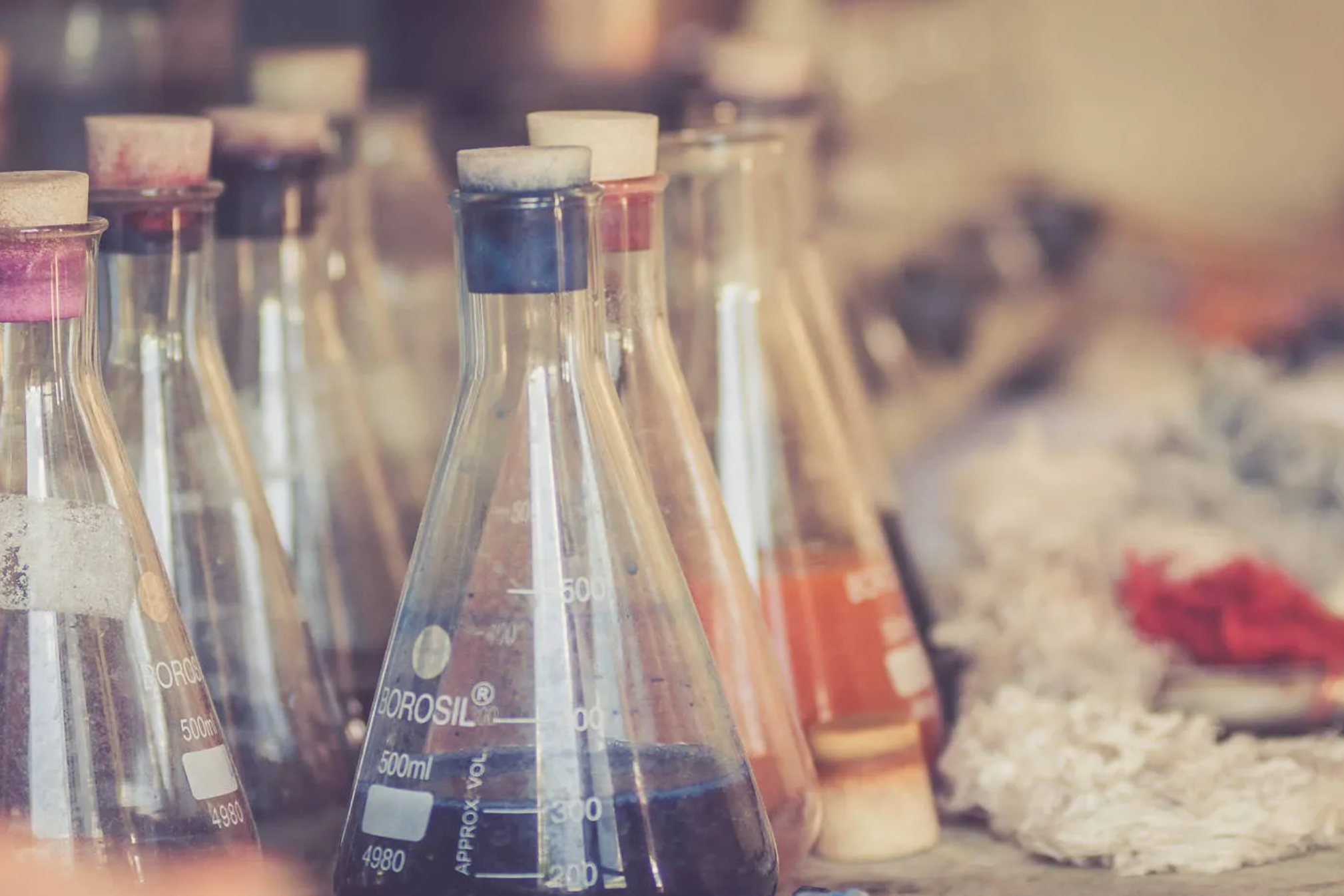
Dyeing
Dyeing yarns is a meticulous and complex process that requires experience and skill. First, several strands are dyed in a lab, and the dye master tries to match the reference color as closely as possible. The lab is filled with jars, copper pots, colorful bowls of exotic pigment powders, and various scales.
Once the ideal formula is obtained, the full strands of wool or silk are placed in large pots. By adding a mordant, the colors are fixed. Commonly used mordants include alum, iron, chrome, and tin. The colorfastness depends on this process.
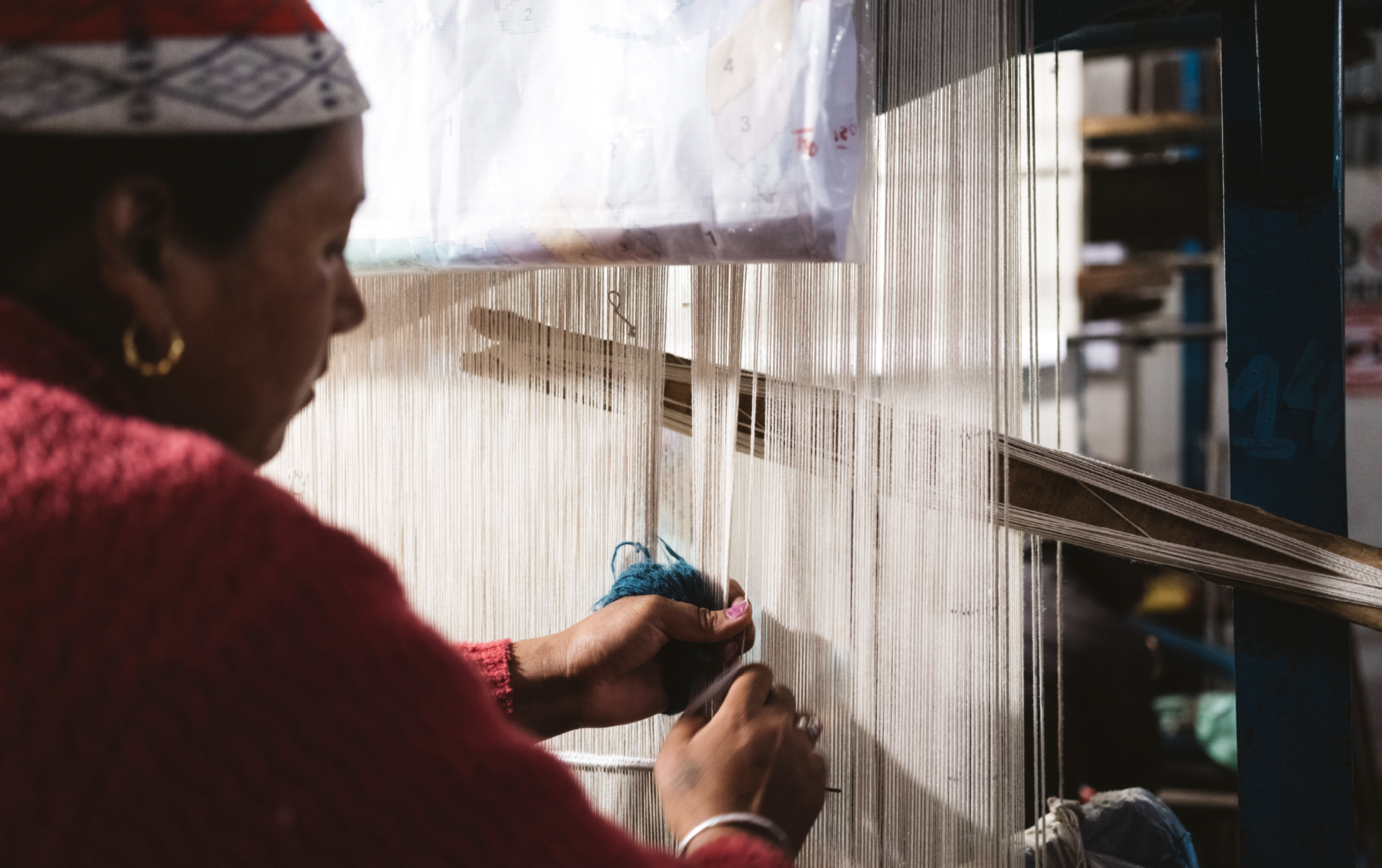
Loom
There are two basic types of looms: a horizontal loom and a vertical loom. Horizontal looms are primarily used by nomads and local weavers, and they are simpler in design. To keep the loom in place, it rests on large pegs that are driven into the ground. There are many types of vertical looms, ranging from simple to complex machines.
In the simplest type of vertical loom, the weaver sits on a board that moves upward as the carpet progresses. In this type of loom, the carpet is usually as long as the loom is tall. This is a major limitation, which is addressed by extending the loom with several options.
The first option is the loom with a movable warp. This involves an uninterrupted loop of warp threads that, as the carpet progresses, drops below the bottom beam and then rises again at the back of the loom. With this type of system, it is possible to make the carpet up to twice as long as the height of the loom. This works for most carpets but remains a limitation for longer formats.
An even more advanced system is the loom with a rolling beam. As the weaving progresses, the carpet is rolled up under the bottom beam. This now makes it possible to knot extra-long formats. Usually, multiple weavers work together in a row on the same carpet.
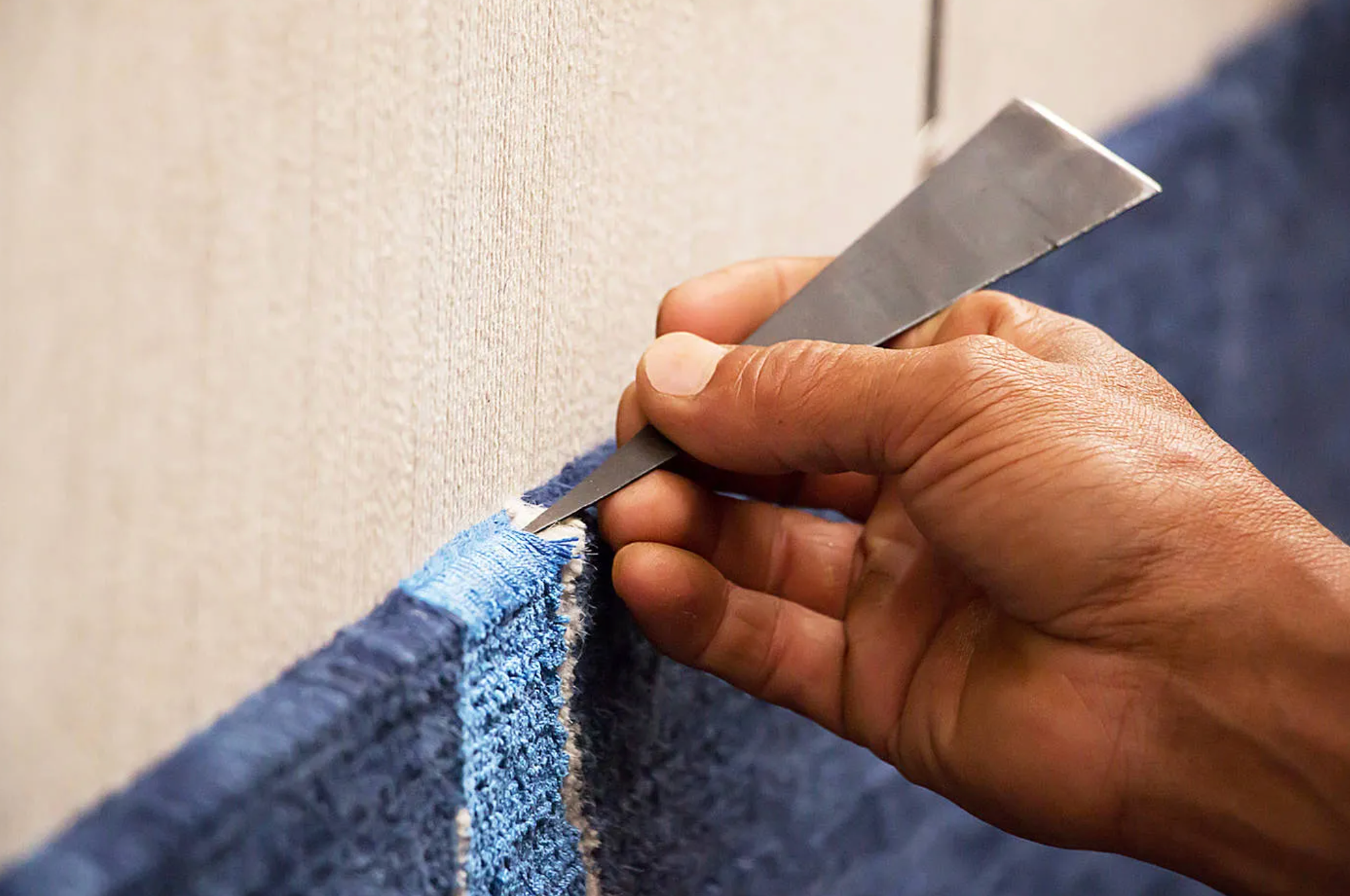
Knotting or Weaving
For workshop carpets or custom-made carpets, part of the preparatory work also involves hiring weavers to create the carpet. Some workshops employ permanent weavers, while others work with subcontractors.
Not all weaving mills work with permanent weavers. Some master weavers have their own specific specialties and conditions and rent out their services to the workshops. As soon as the loom is set up, the knotting process can begin. The weavers start at the bottom of the loom and steadily work their way up. They follow the plan knot by knot, working at a rapid pace. They use three simple tools: the comb, the scissors, and the hooked knife. With the comb, they secure the knots after each row. With the scissors, they trim the pile. With the knife, they first hook around the warp threads or yarn and then quickly cut the knot. This process continues at a fast pace until the carpet is fully completed.
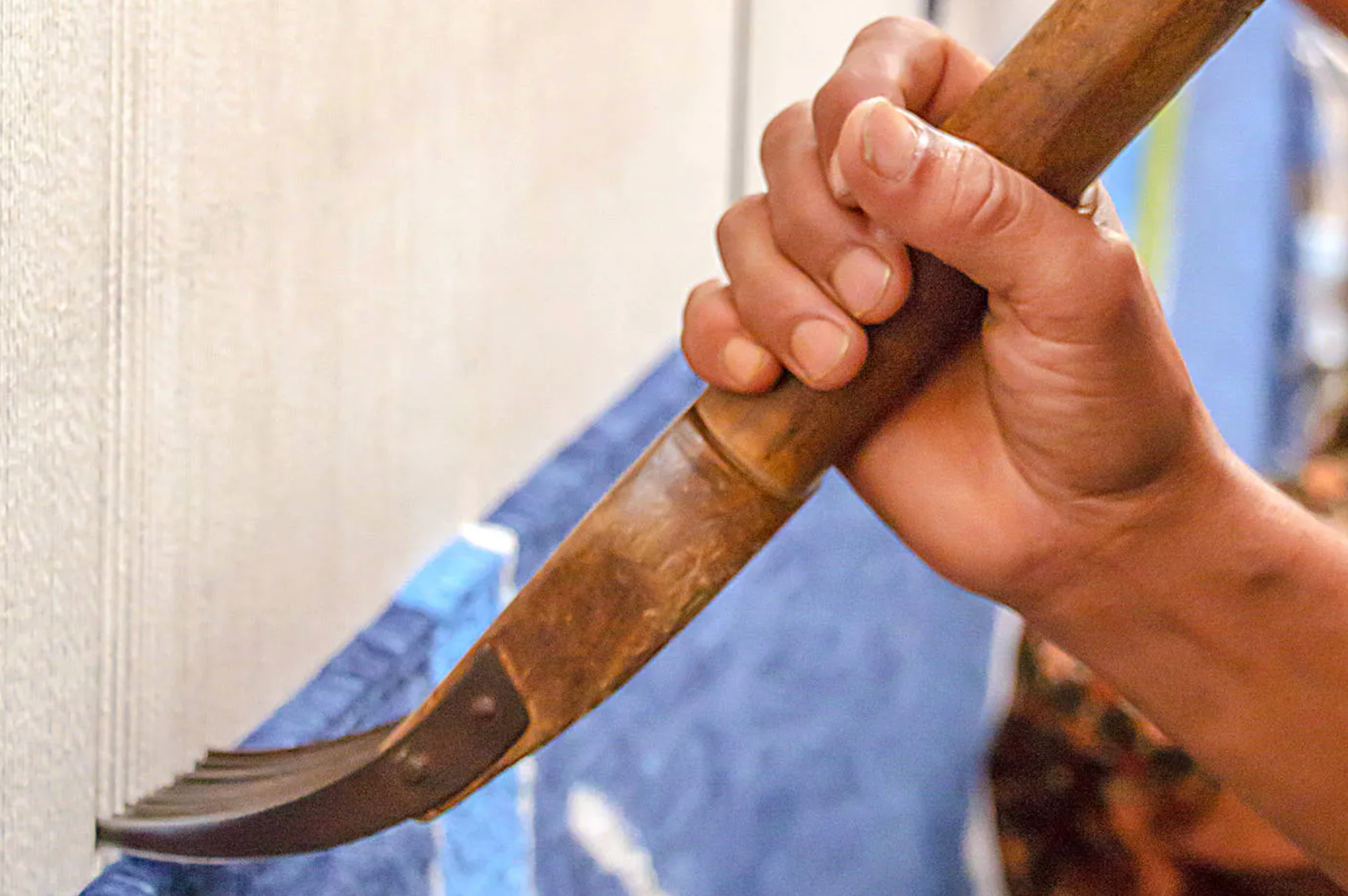
The Year Zero
When the carpet is finally cut loose from the loom, the heaviest and most complex work is finally over. The weavers have given their best, and they are proud of the work they have accomplished. It is always evident that everyone involved in the process has patiently worked toward this moment. The moment when the warp threads are cut is also the moment the carpet is born. There are now loose ends on the carpet that need to be neatly finished. This is done by the weavers creating a kilim border.
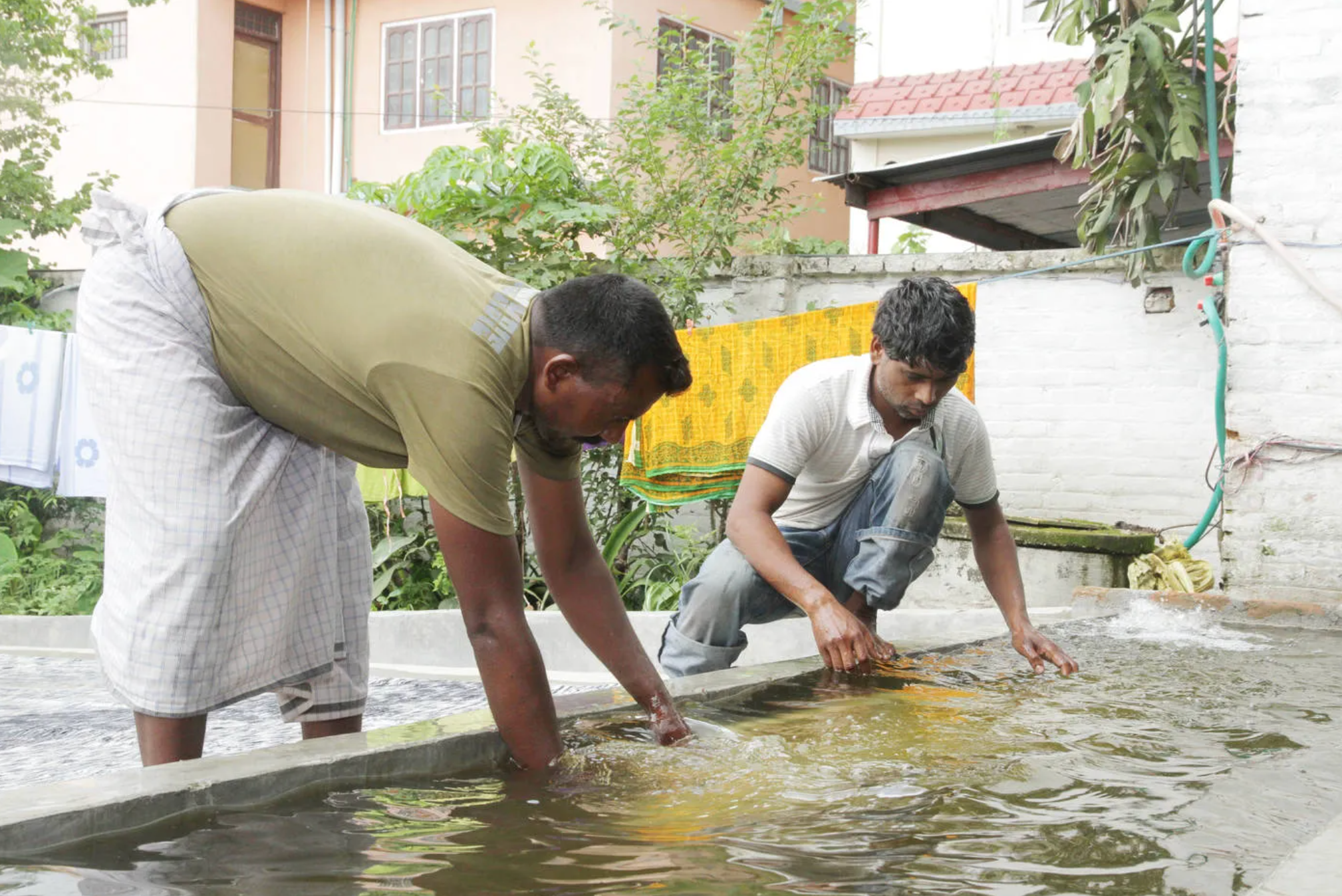
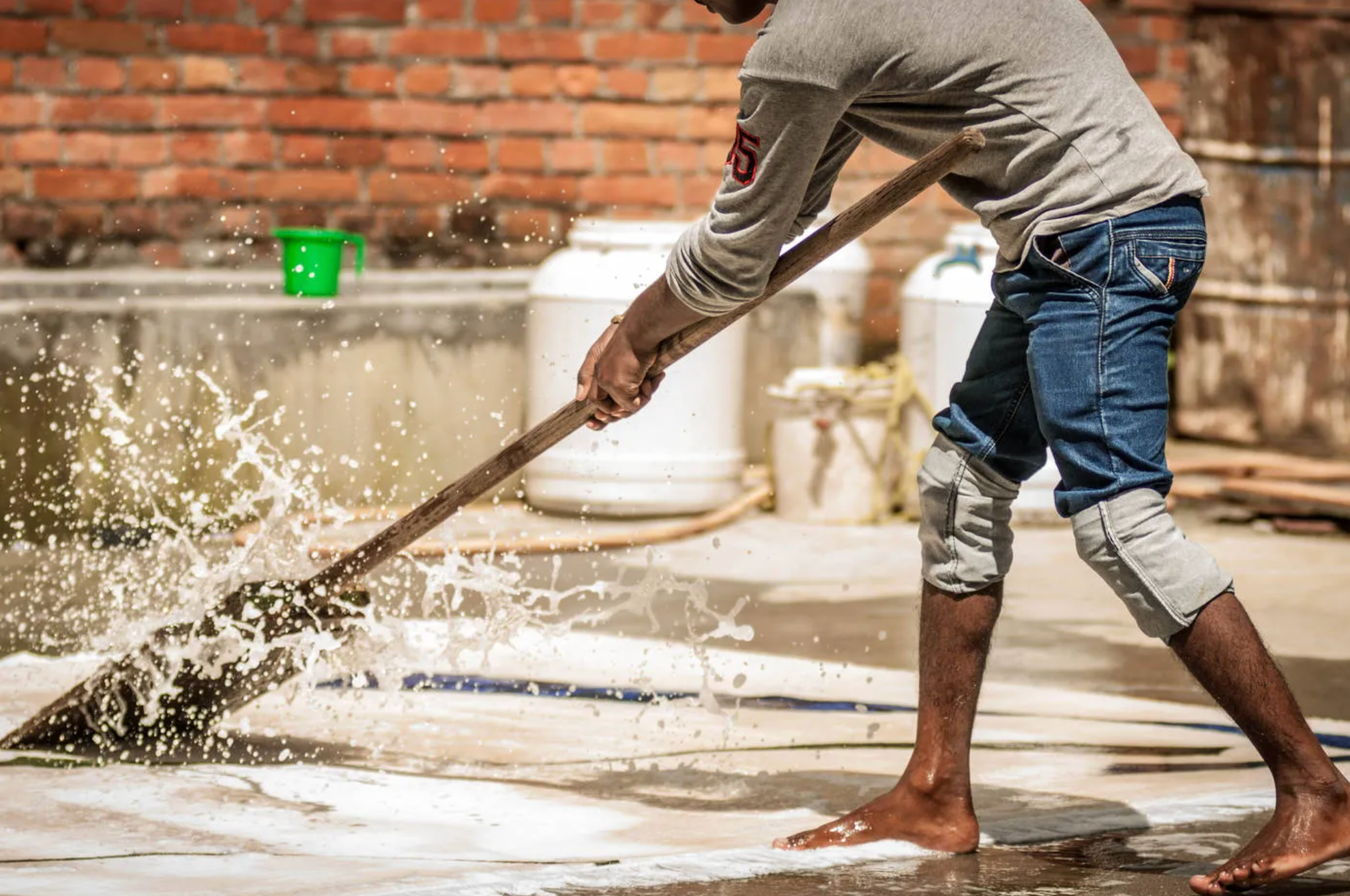
Washing
This process varies from region to region, but the method remains the same. The carpet is fully submerged in basins of pure rainwater or running river water. This serves as an initial test to check if the colors are properly fixed. By washing the carpets in this way, they are freed from all dirt and dust. Afterwards, the carpets are laid flat and scrubbed with a kind of large rake. This ensures that the water can penetrate into and through the fibers.
This process also helps to make the fibers soft again and gives the carpet a beautiful sheen. After the bath, the carpets are laid out in the sun to dry.
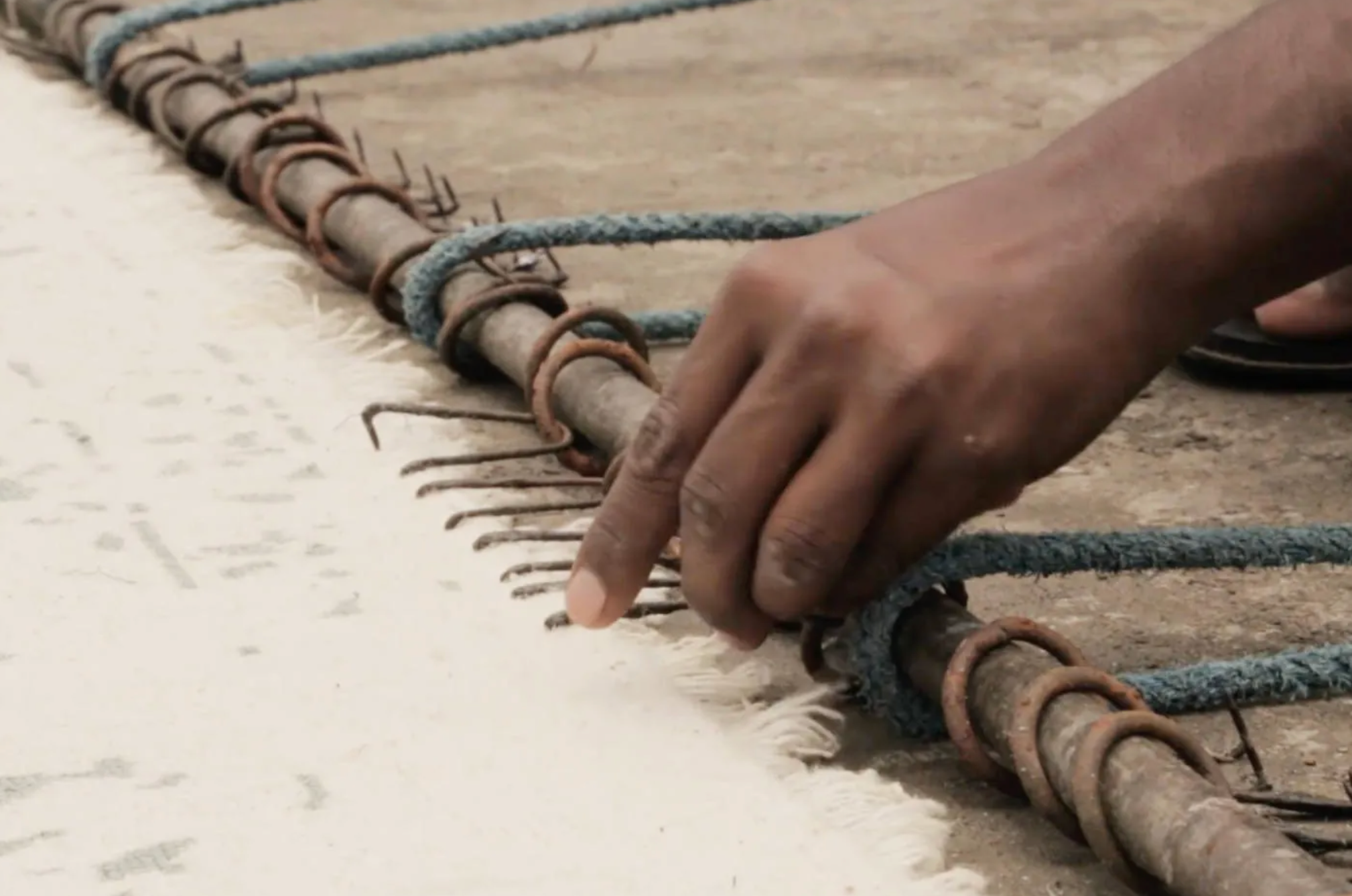
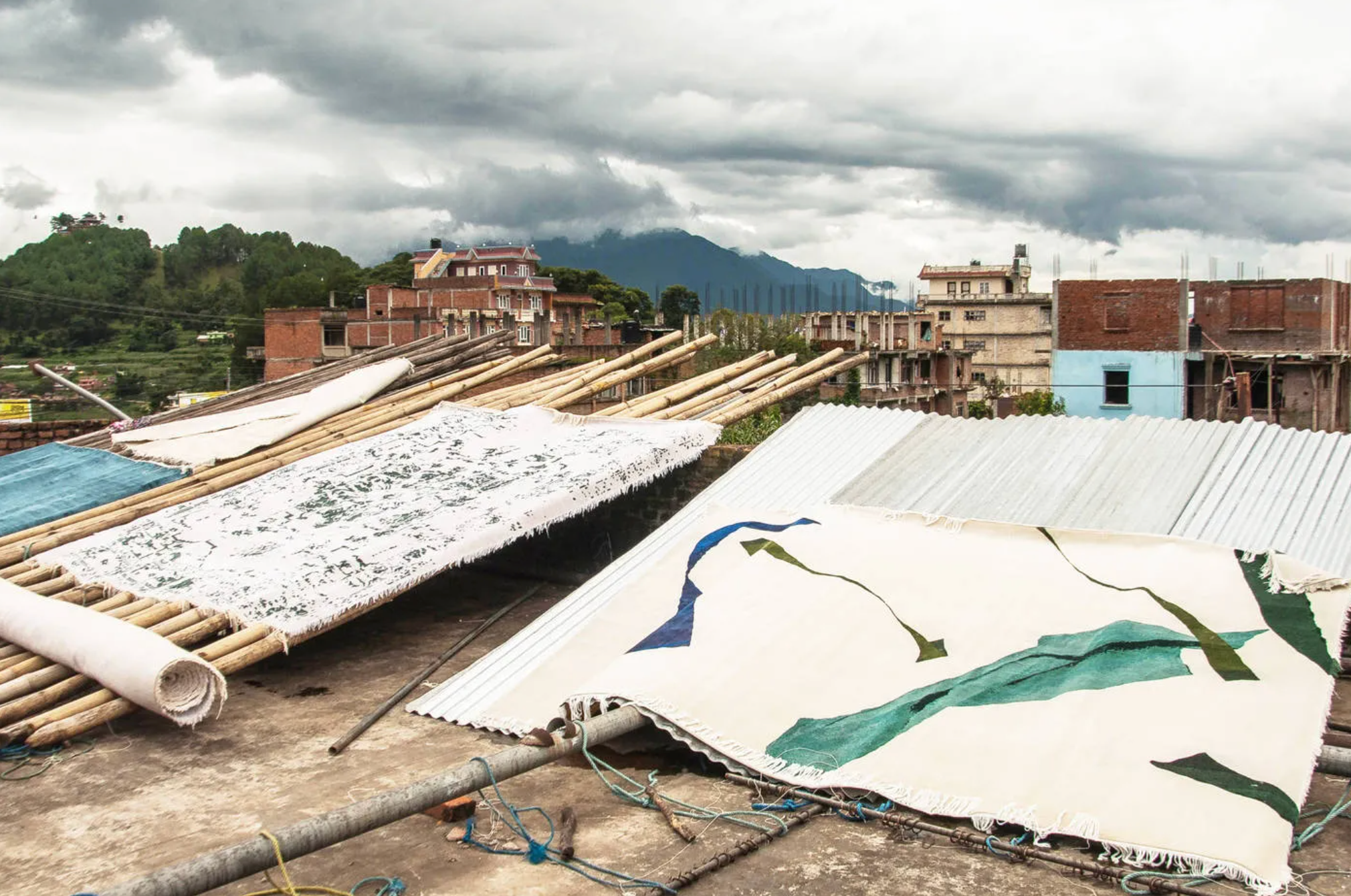
Stretching
After washing, the yarns shrink a little, causing the carpets to lose their shape. Once the carpets are dry, they are inspected and laid flat. Then, the carpets are stretched onto stretching frames. This process restores everything to its proper shape and position.

Finishing
The final phase after stretching is quality control and finishing. If required, the carpets are carved, trimmed, sheared, or bordered. Custom carpets are also weighed and packaged for shipping.
Carving the carpet involves accentuating the contour lines and cutting out patterns with a hand scissor. This is very meticulous work that takes a lot of time but aims to achieve a beautiful final result with more contrast or depth in the carpet.
Bordering the carpet is the finishing touch.